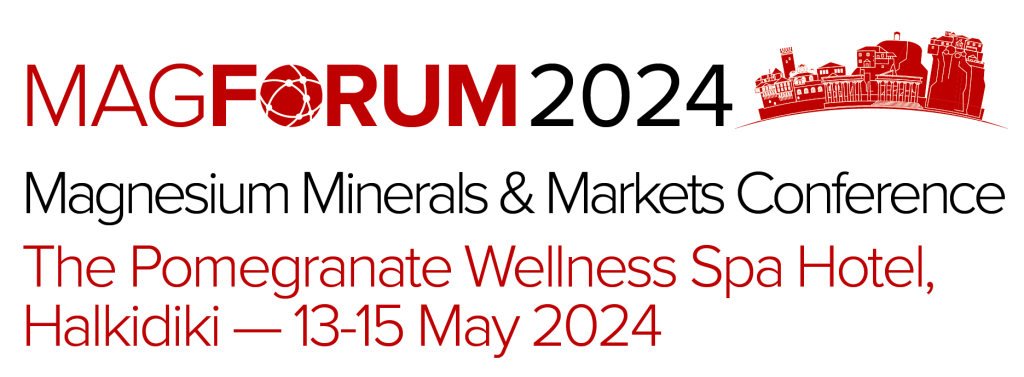
Field Trip is now full
Attendees wishing to be placed on Wait List please contact Ismene ismene@imformed.com
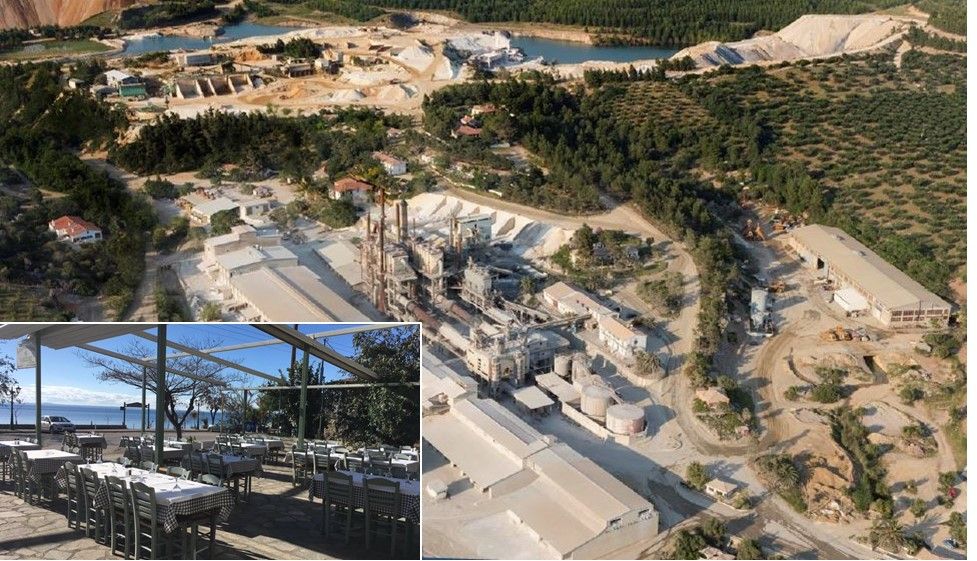
Grecian Magnesite’s operations at Yerakini; Inset: Lunch venue at Kostas Restaurant, Psakoudia Beach
IMFORMED is delighted to be able to offer delegates an exclusive opportunity to visit the operations of Grecian Magnesite at Yerakini, Halkidiki.
The Field Trip takes place the day after the conference, ie. Thursday 16 May (Welcome Reception Monday evening, 13 May; conference on Tuesday and Wednesday 14 & 15 May).
Itinerary*
07:30 Meet Lobby Pomegranate Hotel
07:45 Bus departs from Pomegranate Hotel
08:30 Arrival at Grecian Magnesite, Yerakini; Welcome refreshments & presentation
10:00 Tour of operations
12:00 Departure from Yerakini
12:30 “Mag Art” exhibition inspired by GM’s mines in Yerakini by the Association of Visual Arts Artists of Chalkidiki, at the former GM plant & dock at Yerakini Beach.
13:00 Lunch at Kostas Restaurant, on the sea front at Psakoudia,
15:00 Buses depart to Pomegranate Hotel and Thessaloniki Airport
15:45 Arrive Pomegranate Hotel (16:00 Arrive Thessaloniki Airport)
Please wear clothing and footwear as befits a working industrial site visit.
*subject to change
Overview
Grecian Magnesite (GM) is a privately owned company established in 1959 as a mining and industrial concern. However, the magnesite mining expertise goes back to 1914, when J.G. Lambrinides the “eminence grise” of Greek magnesite and a pioneer mining engineer, started the development and exploitation of most of the magnesite activities in Greece.
GM is a magnesite specialist. The company produces and commercialises caustic calcined magnesia, dead burned (sintered) magnesia, magnesium carbonate (raw magnesite), basic monolithic refractories and dunite (magnesium silicate). A wide range of grades is currently produced, addressing practically all applications where magnesite is used.
GM ranks among the top magnesia producers and exporters in the world, with a staff of around 425 people (in Greece & Turkey) and a turnover of some €65m. In caustic magnesia in particular, our company is a leading world-wide producer both in volumes and spectrum of applications served.
The company’s capacity is close to 200,000 tpa of calcined products and 60,000 tpa of basic monolithic refractories.
The company’s sales value to the European continent represents 70% of its turnover while another 10% corresponds to the Americas and the rest 20% covers Asia, Oceania and Africa.
The company’s major deposits and production facilities are located in Chalkidiki (also spelled Halkidiki), northern Greece, in Eskisehir, central-western Turkey, and in the island of Euboea, central Greece (small scale underground mining operation).
The “Chalkidiki” & “Eskisehir” deposits consist of six main active concessions totalling 80km2. The company also owns “reserve” concessions totalling 16 km2 for future exploitation.
GM magnesite is famous for its whiteness due to the low iron content (as low as 0.02% Fe in the calcined/final product) and the low levels of heavy metals and trace elements. Moreover, low lime content and microcrystalline structure are its additional advantages.
Assets also include a modern R&D facility near Thessaloniki, reserve deposits in Central & Northern Greece, and the headquarters in Athens & Istanbul.
Yerakini, Halkidiki
In the magnesite-rich region of Yerakini, Halkidiki, northern Greece, the ore is extracted by open pit methods.
After blasting, the RoM material is transported by own trucks (dumpers) to the beneficiation departments. In parallel, pre-concentrated magnesite is produced from the RoM old stockpiles via mobile processing units (screening & magnetic separation).
The RoM material is crushed, screened at various size fractions and washed, whereupon it passes through different beneficiation processes (X-ray/camera/laser sorting, magnetic separation, dense media) depending on the desired chemistry of the kiln-feed magnesite.
Overall, at Yerakini, there are 13 optical/X-ray sorters (7 camera, 5 laser and 1 X-ray), two classifying units, four magnetic separation lines and one dense media cyclone installation.
Calcination on site comes next: 3 rotary kilns and 1 shaft kiln, with a combined calcination capacity of 520 tpd, are fed with magnesite to produce caustic calcined magnesia and dead burned magnesia at ~900°C and ~1.800°C respectively.
The caustic calcined magnesia RoK (run of kiln) is then conveyed to the CCM final processing plant for final milling and classification, whereas the dead burned magnesia RoK goes to the DBM final processing plant to produce basic monolithic refractories or specialty DBM powders for high-end applications.
Source: Grecian Magnesite