Refractory magnesia supply trends & developments
Magnesia (magnesium oxide, MgO) is one of the great workhorse refractory raw materials vital to manufacturing a wide range of refractory products, in particular the ubiquitous magnesia-carbon brick, essential to steelmaking worldwide.
Magnesia is sourced mainly from the natural mineral magnesite, and increasingly rarely from synthetic sources such as seawater and magnesium-rich brines.
Title Image Mountain of Magnesite: RHI Magnesita’s Pedra Preta magnesite mine, Brumado, Bahia, supplies feedstock raw material for DBM grades for steel refractories. 2023 production at Brumado was 345,000 tonnes, and a new 140,000 tpa rotary kiln to accelerate vertical integration completed in 2024, is now in ramp-up phase (IMFORMED’s upcoming MagForum 2025 will be visiting this site).
This article by Mike O’Driscoll, Director, IMFORMED, was published in Iron&Steel Today, April 2025; a PDF of the article maybe downloaded here.
There are two principal grades of refractory magnesia: dead burned magnesia (DBM) is produced by calcining magnesite to temperatures 1,500°C to 2,300°C, yielding grades ranging 90-98% MgO, of which >95% MgO is considered high purity; and fused magnesia (FM), produced by fusing magnesite in an electric arc furnace at 2,800°C to 3,000°C yielding grades 96% MgO to >98% MgO.
The refractory magnesia supply sector has been dominated by a reduction in worldwide producers, integration of producers with refractory companies, concern over China’s supply sector, stagnation in steel production, sustainability challenges in decarbonisation, carbon capture, and recycling, and most recently a call for it to be designated a “critical material”.
Supply & trade: down to a few sources
China remains the world’s main producer of magnesite at 13m tonnes in 2024, accounting for almost 60% of world production, and also of DBM and FM production (based on latest US Geological Survey data). Chinese 2024 total exports of DBM were 1.1m tonnes and FM 0.5m tonnes.
Following China, the next main producing countries are Russia (mostly captive), Brazil, Turkey, Austria (mostly captive), and Spain.
Leading import markets for DBM and FM from China are India, USA, Japan and the Netherlands (through its ports for distribution to European consumers).
To exemplify the influence of steelmaking, ie. the primary market for refractory magnesia: in 2024, the USA recorded a significant drop (41% compared to 2023), in imports of Chinese DBM and FM, which has been directly attributed to the decrease in US crude steel production during 2024.
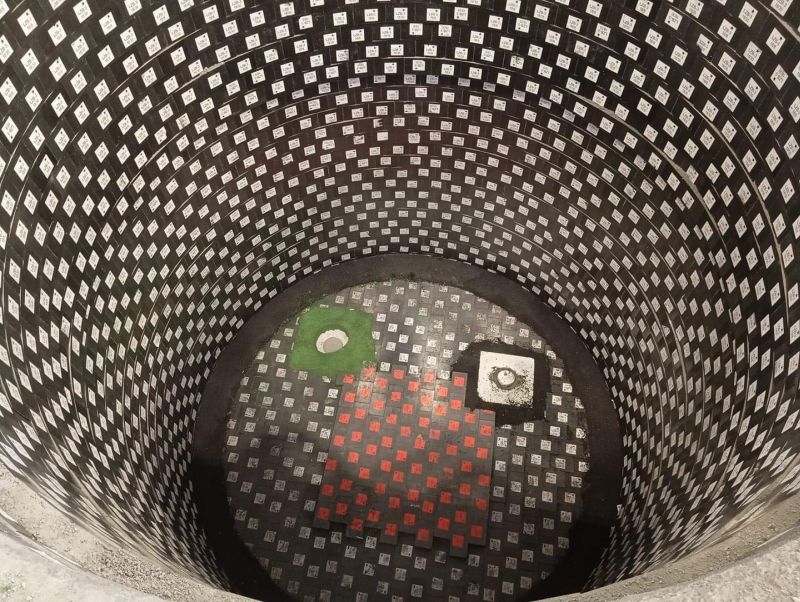
Refractory grade magnesia’s largest use is in steel ladle refractories, as shown here a freshly relined steel ladle with MgO-C bricks. Courtesy RHI Magnesia.
One of the key trends impacting the market for refractory magnesia has been the ever-shrinking group of DBM and FM producers worldwide outside China and Russia (the latter for mostly captive use, and naturally facing export difficulties owing to geopolitical issues).
The main producing countries of DBM refractory grade (all of which host single producers bar Brazil and Turkey) are Australia, Austria, Brazil, Greece, Japan, Mexico, Netherlands, Slovakia, Spain, and Turkey. All are producing natural sourced DBM and are, significantly, integrated with refractory producing owners, apart from the independent synthetic producers in Japan, Mexico, and the Netherlands.
All the trends and developments discussed here will be under the spotlight at IMFORMED’s upcoming MagForum 2025, Salvador, Brazil, 19-21 May – with an exclusive visit to RHI Magnesita’s magnesia operations in Brumado, Bahia
China: oversupply & sector reform
China’s main source of magnesia production is from its north-east Liaoning province, hosting magnesite reserves of 2.51bn tonnes (84% of China, and 22.4% of the world’s reserves).
In 2023, Liaoning’s output was: 19m t MgO refractory materials; 380,000 t MgO chemicals; 1.1m2 building materials.
Liaoning’s provincial government has implemented a succession of measures in recent times to integrate and control magnesite ore mining & processing:
2020: “Provincial Magnesite Mining Rights Integration Plan” reduced mining rights from114 to 56; large/medium-sized mines share increased from 18.4% to 43.9%.
2023: “Implementation Opinions on Promoting the High-quality Development of the Magnesite Industry” & “Special Rectification Plan for the Magnesite Industry in Liaoning Province”.
2024: only 35% mining capacity permitted
2024: MgO plant capacity reduction plan implemented to reduce by 30% – applied to all MgO processing facilities.
2024-25: elimination of all light-burning reverberatory kilns; “This will have a greater impact on the production of some small batches and multiple varieties, and if it is ‘one size fits all’, I am afraid that it will have an impact on the supply of magnesia.” Han Guangqi, Exec. VP, Liaoning Non-metallic Minerals Industry Assoc.
2025: magnesia production capacity upper limits of 15m tpa in Anshan, 8.9m tpa in Yingkou, 0.5m tpa in Dandong
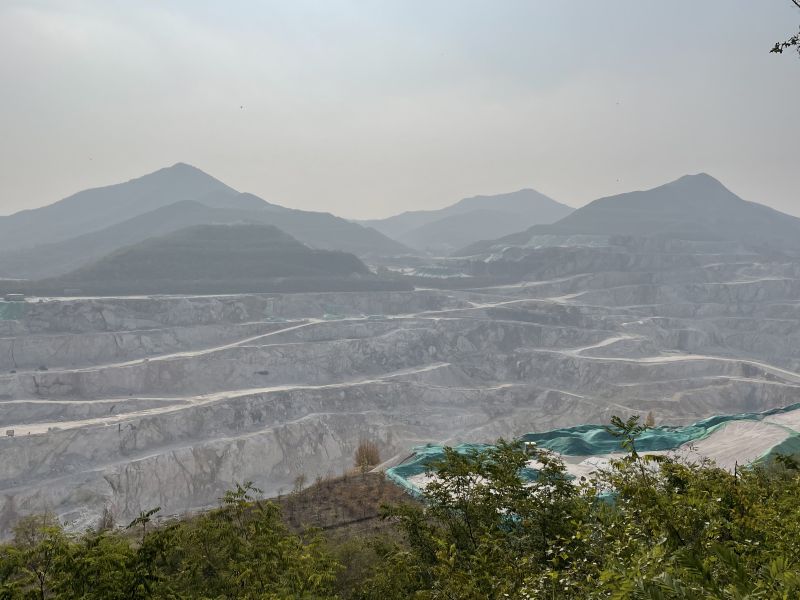
China dominates and continues to influence world refractory magnesia supply. Pictured here is the vast magnesite mine near Haicheng, Liaoning province, China, operated by leading producer Haicheng Magnesite Group Co. Ltd (Haimag) visited by the author in October 2024; production capacity of magnesite ore is 1.69m tpa, and production capacity of all magnesia products is 2m tpa, which includes FM, high-purity DBM, mid-grade DBM, and ordinary grade DBM.
Overall Chinese magnesia production declined in 2024 owing to weak market demand. Since early 2024, magnesite ore price had been rising resulting in increasing difficulty in securing feedstock raw material.
Currently, Chinese DBM supply is sufficient, and market demand flat. With the end of the Spring Festival holiday, most DBM producers have gradually resumed production. Oversupply status remains an issue. However, the government reforms are giving most concern to western traders and consumers over future availability and prices for Chinese magnesia exports.
Owing to rising production costs and sluggish market demand, many Chinese FM producers suspended operations in 2024 (up to 70% of the industry according to some reports).
FM production costs are expected to rise in March 2025, possibly by as much as US$84-113/t with a much anticipated change of electricity price mechanism in Liaoning, possibly raising FM production cost by around US$0.03/kW.
During February 2025, Chinese FOB prices of DBM 95%, lump were at US$345-365/t and that of DBM 96.5%-97%, lump at US$345-365 /t; “mainstream” FOB price of large crystal FM 97.5% lump was US$660-715/t and for FM 98.2% lump at US$865-985 /t, as reported by leading Chinese refractories journal Refractories Window.
Lowering the environmental footprint of magnesia
Like the steel industry, with its processing involving drying and calcination, the magnesia producing industry has a large carbon footprint. The sector is making efforts in reducing CO2 emissions to prepare for 2030 and beyond.
Alternative fuels and materials play an important part in strategies. However, this will not be sufficient, and the sector will ultimately be faced to employ some form of carbon capture/separation.
Leading magnesite producer Grecian Magnesite has made significant efforts to partially replace pet coke with sustainable biomass, which now contributes 25% on energy basis in total (near 80% for (caustic calcined magnesia) CCM production, and 15% or more for DBM, where pet-coke remains the main fuel). There are plans to further intensify biomass utilisation and introduce NG/LNG.
Grecian Magnesite has also been looking into carbon capture by chemical absorption through a series of funded National and EU Research projects using amine-based and carbonate-based capture techniques (Nanocap, CoCCUS and ConsenCUS).
A pilot plant has been constructed for CO2 capture (100 kg/h) at OMV Petrom in Romania, and another pilot plant at Grecian Magnesite’s Yerakini site became operational in January 2025.
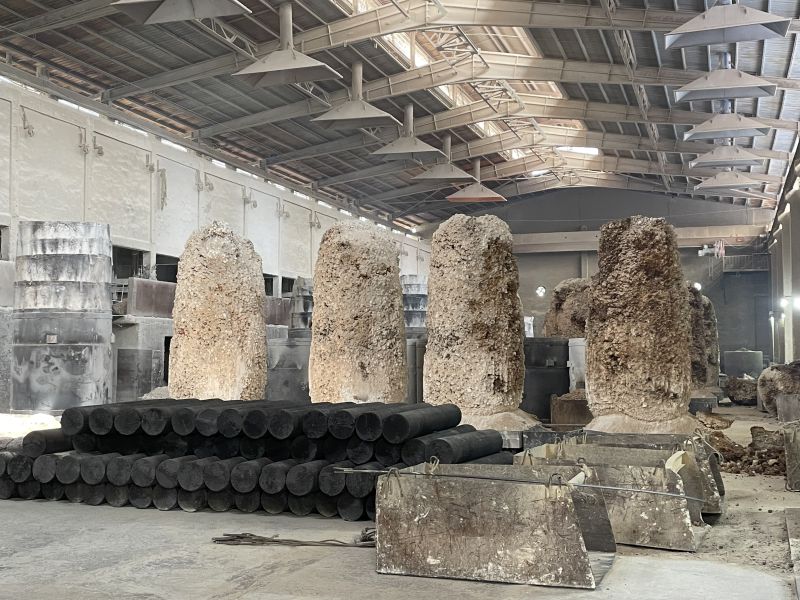
“Crystallised electricity”: Electrofused magnesia ingots cooling before being broken and sorted into grades, with new graphite electrodes in foreground for use in the EAFs, at Haicheng Magnesite Group Co. Ltd (Haimag)’s plant in Haicheng, Liaoning province, China.
Future demand from European steel
In the EU, steel production and consumption are expected to grow in line with GDP over the next five years, to an estimated 141m tonnes and 143m tonnes by 2028, respectively (according to a 2024 report by Project Blue).
Magnesia refractories have a higher consumption in EAF (mainly in steel ladle slag zones) which are being used increasingly to recycle scrap steel as part of the overall drive to sustainability within the steel industry.
Project Blue has identified 35m tpa of new steel capacity in the EU using the EAF route by 2030, and another 10m tpa that could come onstream in the early 2030s, replacing blast furnaces and mostly dedicated to steel long products.
This all indicates good prospects for magnesia refractory demand. But can European magnesia supply meet this demand?
Will magnesia go “critical”?
Since December 2024, world leading magnesia and refractory producer RHI Magnesita, with support from Euromines (the EU trading organisation representing metals and minerals producers), has been calling for magnesite and magnesia to be designated “critical materials”.
The organisations hosted the “Magnesia Cocktail” in Brussels on 9 December during Raw Materials Week 2024, in a move to emphasise the critical role of magnesite and magnesia as raw material in Europe’s green transition and in building industrial competitiveness.
The event brought together industry leaders, policymakers, and experts to underline the need for immediate action to include magnesite and magnesia on the EU’s list of Critical Raw Materials (CRM) to ensure raw material supply security for Europe.
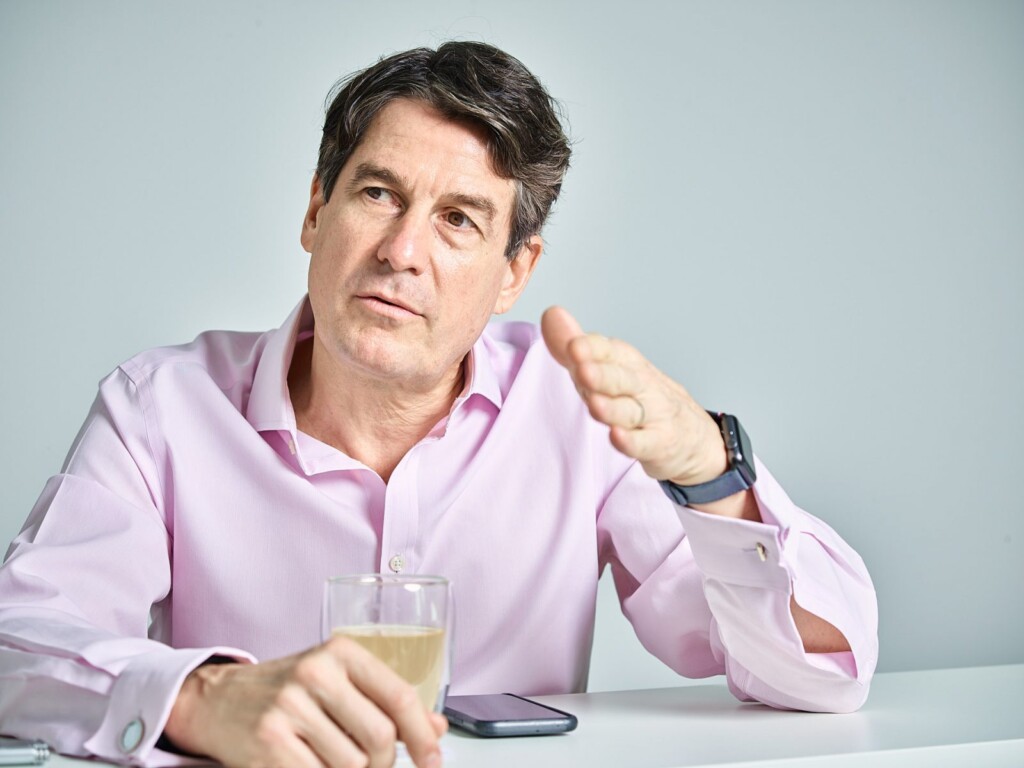
“Recognizing its [magnesia’s] importance is essential to strengthening Europe’s resilience and leadership in the green transition.” Stefan Borgas, CEO, RHI Magnesita. Courtesy RHI Magnesita
Stefan Borgas, CEO of RHI Magnesita, said: “Magnesia, derived from Magnesite, is the backbone of refractories required for critical raw material processing and decarbonization efforts. This is essential particularly in steelmaking, cement and glass production. It is a catalyst for over 50% of strategic raw materials for refractories and 30% of critical raw materials. Recognizing its importance is essential to strengthening Europe’s resilience and leadership in the green transition.”
Project Blue, the London and Cape Town-based provider of critical mineral market intelligence, conducted a Magnesia Industry Study for Euromines in late 2024 and concluded: “Given the challenges and the future growth of magnesia demand, the ambitions of net zero in Europe will be difficult to achieve without a secure and stable domestic supply of magnesia.”
The report highlighted that the ability of European magnesia producers to meet domestic demand growth could be hampered by a “confluence of challenges”, including high energy prices, a lack of alternative fuel sources, technological and financing obstacles to meet sustainability and decarbonisation requirements.
These challenges have driven escalating costs for European producers over the last five years, resulting in operations closing and reducing their supply base. Most recently, in 2022, Premier Periclase Ltd, high purity DBM producer in Republic of Ireland ceased operations.
As a result, European imports of magnesia products have increased, especially from China as they are very competitively priced relative to European production.
In other words, there is a strong and vulnerable reliance by European consumers and their end customers, particularly the steel industry, on overseas sources of refractory magnesia.
This has now forced the hand of the European industry to pursue “critical” status for magnesia. The industry now awaits a response from the EC.
Among the presentations at MagForum 2025, Salvador, 19-21 May will be Jessica Roberts, Research Director, Project Blue, UK speaking on “Magnesia market outlook: geopolitical trends & critical mineral status”
Excellent article, very comprehensive and straight to the point. The energy costs and CO2 release when you break down the carbonate structure may impose some new challenges in the future.